How to develop cost-effective materials that are safe and durable
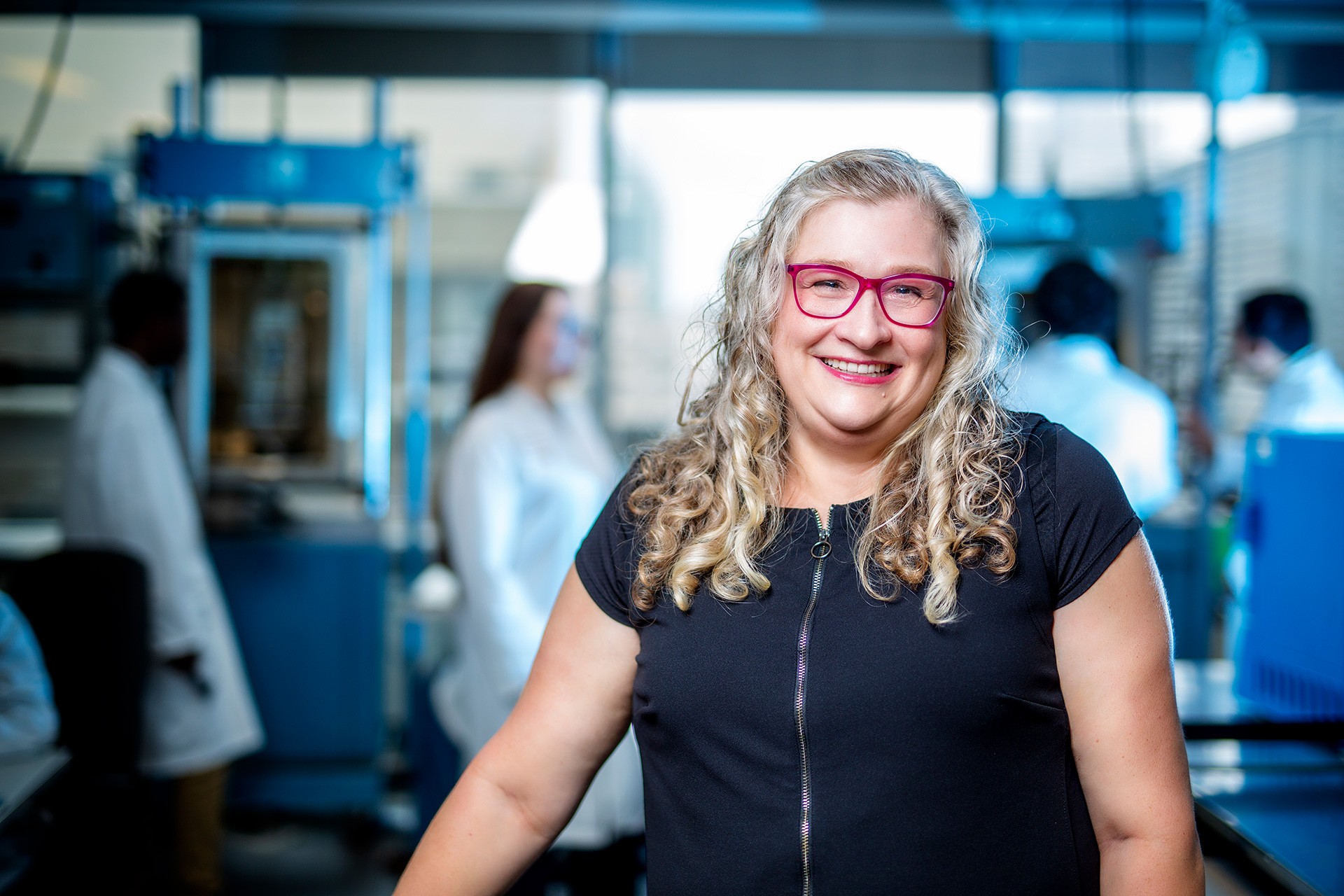
Materials science is at the heart of contemporary manufacturing and product development. New advances within the discipline often provide cutting-edge solutions to consumer problems and affect the future of technology in general. Developing innovations for materials takes time, though, and money can be wasted in the process.
Paula Wood-Adams, professor in the Department of Chemical and Materials Engineering, and her team of six students — three PhD, two undergraduate and a postdoctoral fellow — develop techniques to understand and modify the properties of materials. One of the aims of their research is to remove unnecessary and costly trial and error.
“Knowing how a material is going to behave, or not, eliminates the unknown,” explains Wood-Adams. “It allows you to make important decisions that will affect the quality and safety of a product.”
Wood-Adams developed her appreciation for material properties while working in industry. After earning her bachelor’s degree in chemical engineering at the University of Alberta, she was struck by how little material processes were understood and how much waste was produced as a result.
Today, Wood-Adams’ work is guided by her interests, as well as those of her students. In addition to being the Gina Cody School of Engineering and Computer Science's resident expert on advanced materials, she is also the dean of Concordia University’s School of Graduate Studies.
“When I first came to Concordia in 2001, it was rare to see a lab with graduate students in it,” she says. “Now, the amount of students in master’s and PhD programs is a testament to the volume, as well as the breadth, of research being done at the university.”
Together, Wood-Adams and Keroles Riad, a PhD candidate in the Individualized Program, are developing a new set of photocurable polymers for stereolithography 3D printing. The project addresses two challenges: the material’s photostability and its mechanical properties. Since the material is lightweight — and 3D printing can easily create complex shapes — increasing its durability will allow it to be used in high stress conditions. This initiative is of particular interest to the aerospace industry.
Wood-Adams and her team are also working on projects that will identify processes of diffusion of polymers and solvents, die drool, and self-healing conductive polymers.