STEM SIGHTS: The Concordia student who ice-proofs airplanes

Whether you were born and raised in Montreal or came to the city as a student, chances are you have experienced flight delays due to icing.
While ice can pose issues if it forms on runway surfaces, it is also a particularly nasty problem on the bodies of airplanes.
Enter Navid Sharifi, a PhD candidate in the Department of Mechanical, Industrial and Aerospace Engineering at Concordia.
His PHOBIC2ICE project is a collaboration between research engineers in Canada and Europe aiming to find surface engineering solutions for aviation-related icing problems.
“Icing poses a great threat in aerospace and aviation sectors both in terms of damage to equipment and risk of accidents that can cost the lives of passengers and crew,” Sharifi explains.
That’s why his team is working to create coatings that can be applied to the outside of an airplane body to make them resistant to ice formation. Whether a coating is extremely water-repellent or just very slippery, if it performs well in an icing situation, it’s considered icephobic.
PHOBIC2ICE won the 2017 Consortium for Aerospace Research and Innovation in Canada Innovative Project of the Year Award at their 3rd National Research Forum, held on August 8 and 9 in Vancouver.
‘Our coatings enable companies to mitigate icing problems’
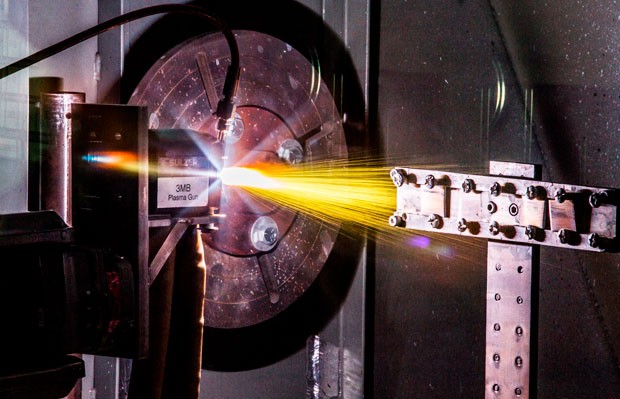
How does this specific image (above) relate to your research at Concordia?
Navid Sharifi: Ice accretion on aerodynamic surfaces during flight poses a major threat to aircraft. I’m currently working with an international project to develop novel micro- and nano-engineered coatings that can be applied to the surface of aircraft bodies to prevent or delay ice formation. I work on developing such coatings using thermal spray technology, in particular a cutting-edge technique called suspension plasma spraying.
The equipment shown in the picture is a thermal plasma spray system. You can see just the plasma torch attached to a robotic arm used to operate it. This system can be used to deposit almost any engineering material on a surface. I specifically use it to deposit high-temperature advanced ceramics and alloys and for micro-structured functional coatings.
What is the hoped-for result of your project? And what impact could you see it having on people's lives?
NS: Icing poses a great threat in aerospace and aviation sectors both in terms of damage to equipment and risk of accidents that can cost the lives of passengers and crew. Our coatings will enable aerospace companies to mitigate icing problems and not only eliminate the risk of fatal icing-related incidents but also minimize the associated damage, protection and repair costs.
Such coatings can be used on aircraft aerodynamic parts, sensors, control systems and even engine parts and can protect them from icing hazards in harsh environmental conditions.
What are some of the major challenges you face in your research?
NS: One of the major challenges is to convert research results that aren’t necessarily ready for practical application into real-world technologies that industry can directly implement. This is particularly the case when working with the aerospace industry because of all their meticulous testing and verification procedures.
My research also has several phases, including feedstock material preparation, coating generation and optimization, characterization and performance evaluation. The wide range of techniques, processes and systems that I need to work with poses an additional challenge. Dealing with all this requires a lot of time and effort but, ultimately, it is very rewarding because it helps me improve my skills and learn about different areas of research.
What person, experience or moment in time first inspired you to study this subject and get involved in the field?
NS: Most of that credit goes to my PhD supervisor, Ali Dolatabadi. He accepted me onto his team and, through continuous guidance and support, allowed me to experience and explore different aspects of research.
Having the freedom to investigate your ideas and make use of your creativity is an opportunity not very often provided to researchers at my level.
How can interested STEM students get involved in this line of research? What advice would you give them?
NS: Our team always welcomes students who want to learn more and gain experience. We have undergraduate and graduate students doing internships or projects with us, and often they come from diverse scientific backgrounds, including materials and mechanical engineering, programming and electronics.
What do you like best about being at Concordia?
NS: I like the dynamism and synergy of Concordians. People are always supportive and open to collaboration, and that, in my opinion, is what gives the university an advantage in terms of education and research.
Is there any partner, agency or other funding/support attached to your research?
NS: This project is supported by the Consortium for Aerospace Research and Innovation in Canada (CARIC), the Natural Sciences and Engineering Research Council of Canada and the European Commission.
Find out more about Concordia’s Thermal Spray and Multiphase Flow Laboratories.