Concordia prof responds to the lockdown by making at-home printmaking presses for students and artists
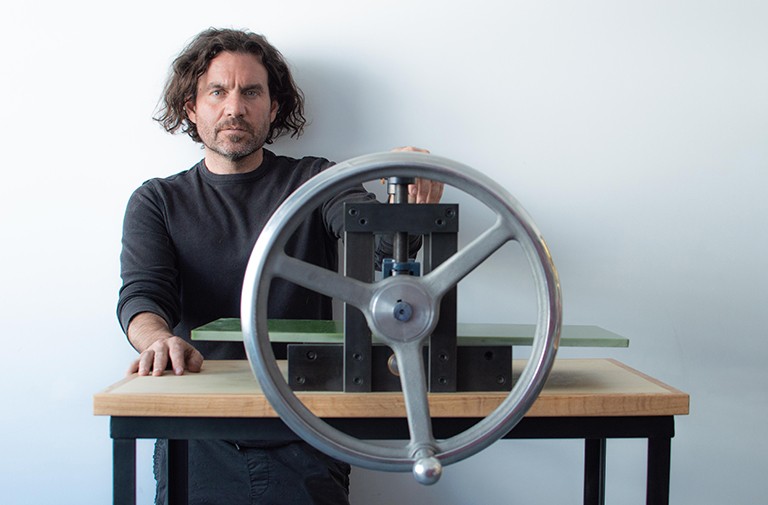
Mitch Mitchell is an interdisciplinary artist and associate professor of print media in the Department of Studio Arts
When the COVID-19 pandemic started last year and universities began to lock down, I found myself fabricating handmade printmaking presses for artists in and outside of Concordia.
Why? As educators, we were faced with the inability to teach printmaking practices efficiently. Students were thrust into a world of printing at home in their kitchens, bathrooms and bedrooms using nothing but their hands and feet to transfer an image onto paper.
Lithography and intaglio are the most difficult without presses, as relief and silkscreen are more easily converted to at-home printing. By the end of the winter 2020 term, students and instructors were exhausted — and still are — but we kept pushing forward.
Cheaper, smaller, more efficient
The idea started when through email I joined faculty from various institutions to create a research group loosely called GraphicThinkTank. We asked, what was the future of printmaking without a shared community space? Out of this, the greatest issue was the lack of access to presses, fundamentals and physical knowledge of the core tool in any print shop, after the artist.
Out of curiosity and a bit of fear of the upcoming year with Zoom learning, I suggested fabricating small portable presses for students. Despite being practically difficult due to the lack of facilities, pre-prep and knowledge of engineering, technical machining and function, I decided to try.
At the time, I was not feeling 100 per cent with my own practice knowing everything else going on in the world. Faculty and students were emailing me with questions about how print could exist outside of a community shop. I redirected my research and used my historical knowledge of printmaking, presswork, mechanical engineering and background in manual machining and woodworking to conceive of a press design that would solve three basic problems with modern presses: they are big and heavy and cost a lot to ship; they are labour-intensive to make; and they are extremely expensive.
I set out to redesign the press from the ground up using my studio and my grandfather’s metal lathe that I had shipped from Chicago. The result is a far cheaper, smaller, lighter, more efficient and easy-to-make press than is commercially available — the only one available with its specs in Canada.
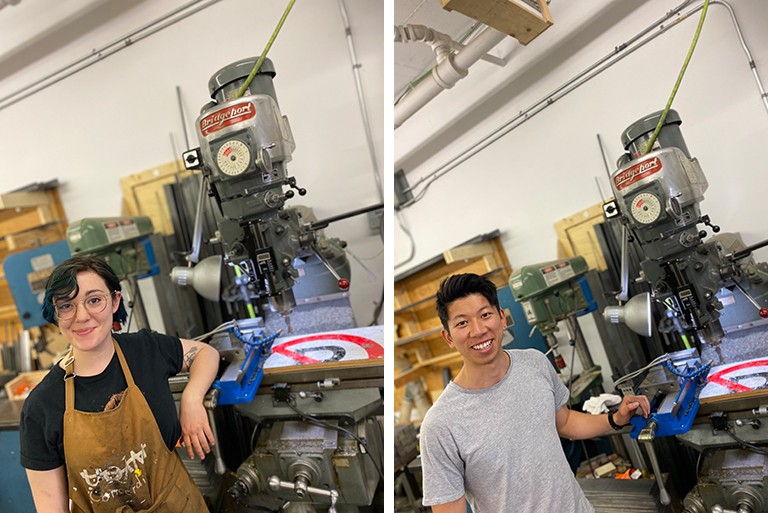
‘I was shocked with the level of interest’
I began the project as a way to refocus my studio practice to get my mind off the surreal world we were living in at the time. I wanted to figure out if there was a better, more efficient and cost-effective way of producing a tabletop printmaking press for our students during the university lockdown.
A lot has happened since then, and our efforts are changing things quite a bit for the Canadian arts community. What started as a few posts on Instagram of the project turned into a high level of interest. I was honestly shocked with the excitement and sales of my presses from around Canada and the world.
Because of this, I expanded and decided that for every 10 presses sold I would donate one to a creative community in need. I am excited to say that I am already making four presses for future donations.
I have also designed another press that has the ability to be “printed” via email chain to any place that has a CNC (computer numerical control) mill and lathe. This will allow for any university or print community to go immediately into production for a fraction of the cost.
What’s next?
More recently, I started a paid apprenticeship program for print media students who have lost their jobs during the pandemic. This initiative is to not only provide sustainable work until things open up more but also to educate them on the process of making a press via machining, knowledge that I learned as a teenager that I have used in my everyday studio and teaching practice.
So far, students are really excited to learn all the planning, techniques and history of the process of manual machining. This apprenticeship is open to individuals who want to learn no matter their technical history, knowledge level and skill. I am excited to have Maddi Berger, a current printmaking BFA student, and Alex Chu, a graduating student in the same program, as my first two interns.
By posting process videos on Instagram, students have also become very interested in learning more. I have been wanting, for a long time, to create a yearlong six-credit course in collaboration with the Print Media program and the metal fab shop in the EV Building. My dream is that in term one they would make all the tools and their own printmaking press and in the second they would use only these tools to make art. I have more than 30 students wanting to register as a special projects class when and if we can get it scheduled and vetted.
Overall, it has been a very exciting and exhausting process that came out of a surreal time.
Follow Mitchell Press Works on Instagram and find out more about Concordia’s Department of Studio Arts.